SMT utilitza pasta de soldadura convencional per reflux d'aire per anàlisi de cavitats i solució (edició Essence 2023), t'ho mereixes!
1 Introducció

En el muntatge de la placa de circuit, primer s'imprimeix pasta de soldadura a la placa de soldadura de la placa de circuit i després s'hi fixen diversos components electrònics. Finalment, després del forn de refusió, les perles d'estany de la pasta de soldadura es fonen i tot tipus de components electrònics i la placa de soldadura de la placa de circuit es solden junts per aconseguir el muntatge de submòduls elèctrics. La tecnologia de muntatge superficial (SMT) s'utilitza cada cop més en productes d'embalatge d'alta densitat, com ara paquets de nivell de sistema (SiP), dispositius Ballgridarray (BGA) i dispositius Power Bare Chip, paquets quadrats sense pins plans (Quad AATNo-lead, coneguts com a QFN).
A causa de les característiques del procés i materials de soldadura amb pasta de soldadura, després de la soldadura per refusió d'aquests dispositius de gran superfície de soldadura, hi haurà forats a la zona de soldadura, cosa que afectarà les propietats elèctriques, tèrmiques i mecàniques del rendiment del producte, i fins i tot conduirà a una fallada del producte. Per tant, millorar la cavitat de soldadura per refusió de pasta de soldadura s'ha convertit en un problema tècnic i de procés que s'ha de resoldre. Alguns investigadors han analitzat i estudiat les causes de la cavitat de soldadura de boles de soldadura BGA i han proporcionat solucions de millora. La zona de soldadura del procés convencional de soldadura per refusió de pasta de soldadura amb QFN superior a 10 mm2 o la solució de xip nu de la zona de soldadura superior a 6 mm2 és insuficient.
Utilitzeu la soldadura Preformsolder i la soldadura al forn de reflux al buit per millorar el forat de soldadura. La soldadura prefabricada requereix un equip especial per apuntar el flux. Per exemple, el xip es desplaça i s'inclina considerablement després de col·locar-lo directament sobre la soldadura prefabricada. Si el xip de muntatge de flux es refloda i després es apunta, el procés augmenta en dues reflotacions, i el cost del material de soldadura i flux prefabricat és molt més alt que el de la pasta de soldadura.
L'equip de reflux al buit és més car, la capacitat de buit de la cambra de buit independent és molt baixa, el rendiment econòmic no és elevat i el problema de les esquitxades d'estany és greu, cosa que és un factor important en l'aplicació de productes d'alta densitat i pas petit. En aquest article, basat en el procés convencional de soldadura per reflux amb pasta de soldadura, es desenvolupa i s'introdueix un nou procés de soldadura per reflux secundari per millorar la cavitat de soldadura i resoldre els problemes d'unió i esquerdes del segellat de plàstic causats per la cavitat de soldadura.
2 Cavitat de soldadura per reflux d'impressió en pasta de soldadura i mecanisme de producció
2.1 Cavitat de soldadura
Després de la soldadura per refusió, el producte es va provar amb raigs X. Es va descobrir que els forats a la zona de soldadura amb un color més clar eren deguts a una soldadura insuficient a la capa de soldadura, tal com es mostra a la Figura 1.
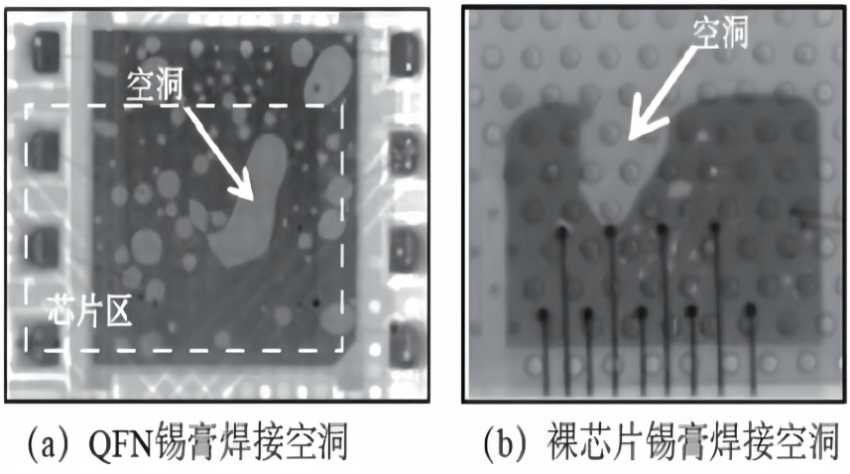
Detecció de raigs X del forat de la bombolla
2.2 Mecanisme de formació de la cavitat de soldadura
Prenent com a exemple la pasta de soldar sAC305, la composició i la funció principals es mostren a la Taula 1. El flux i les perles d'estany s'uneixen en forma de pasta. La relació en pes entre el soldadura d'estany i el flux és d'aproximadament 9:1, i la relació en volum és d'aproximadament 1:1.
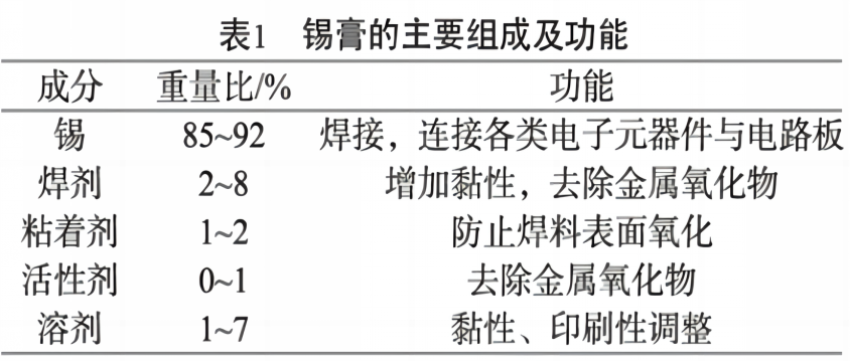
Després d'imprimir i muntar la pasta de soldadura amb diversos components electrònics, la pasta de soldadura passarà per quatre etapes de preescalfament, activació, reflux i refredament quan passi pel forn de reflux. L'estat de la pasta de soldadura també és diferent amb diferents temperatures en les diferents etapes, com es mostra a la Figura 2.
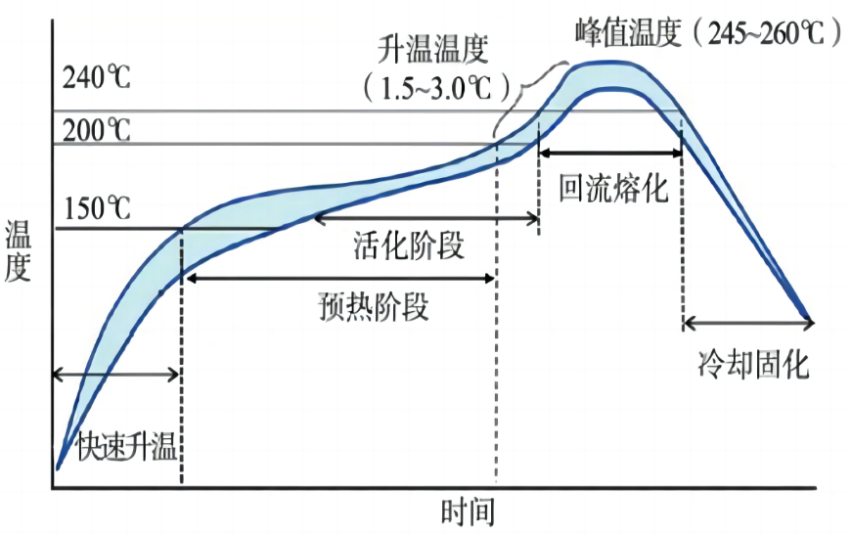
Referència de perfil per a cada àrea de soldadura per refusió
En l'etapa de preescalfament i activació, els components volàtils del flux de la pasta de soldadura es volatilitzaran en gas quan s'escalfen. Al mateix temps, es produiran gasos quan es retiri l'òxid de la superfície de la capa de soldadura. Alguns d'aquests gasos es volatilitzaran i abandonaran la pasta de soldadura, i les perles de soldadura es condensaran fortament a causa de la volatilització del flux. En l'etapa de reflux, el flux restant a la pasta de soldadura s'evaporarà ràpidament, les perles d'estany es fondran, una petita quantitat de gas volàtil de flux i la major part de l'aire entre les perles d'estany no es dispersaran a temps, i els residus a l'estany fos i sota la tensió de l'estany fos formen una estructura de sandvitx d'hamburguesa i són atrapats per la placa de soldadura de la placa de circuit i els components electrònics, i el gas embolicat a l'estany líquid és difícil d'escapar només per la flotabilitat ascendent. El temps de fusió superior és molt curt. Quan l'estany fos es refreda i es converteix en estany sòlid, apareixen porus a la capa de soldadura i es formen forats de soldadura, com es mostra a la Figura 3.
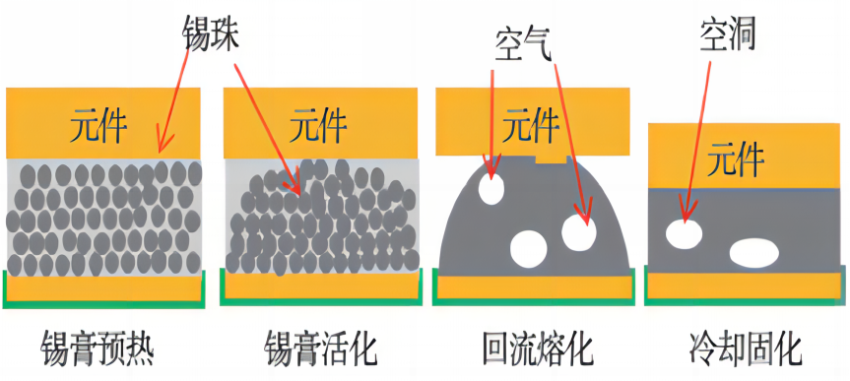
Diagrama esquemàtic del buit generat per la soldadura per refusió de pasta de soldadura
La causa principal de la cavitat de soldadura és que l'aire o el gas volàtil embolicat a la pasta de soldadura després de la fusió no es descarrega completament. Els factors que influeixen inclouen el material de la pasta de soldadura, la forma d'impressió de la pasta de soldadura, la quantitat d'impressió de la pasta de soldadura, la temperatura de reflux, el temps de reflux, la mida de la soldadura, l'estructura, etc.
3. Verificació dels factors d'influència dels forats de soldadura per refusió amb pasta de soldadura
Es van utilitzar proves de QFN i de xip nu per confirmar les principals causes dels buits de soldadura per refusió i per trobar maneres de millorar els buits de soldadura per refusió impresos amb pasta de soldadura. El perfil del producte de soldadura per refusió de QFN i de pasta de soldadura per xip nu es mostra a la Figura 4, la mida de la superfície de soldadura QFN és de 4,4 mm x 4,1 mm, la superfície de soldadura és una capa d'estany (100% estany pur); la mida de soldadura del xip nu és de 3,0 mm x 2,3 mm, la capa de soldadura és una capa bimetàl·lica de níquel-vanadi polvoritzada i la capa superficial és de vanadi. El coixinet de soldadura del substrat era d'or per immersió electrolítica de níquel-pal·ladi i el gruix era de 0,4 μm/0,06 μm/0,04 μm. S'utilitza pasta de soldadura SAC305, l'equip d'impressió de pasta de soldadura és DEK Horizon APix, l'equip de forn de reflux és BTUPyramax150N i l'equip de raigs X és DAGExD7500VR.
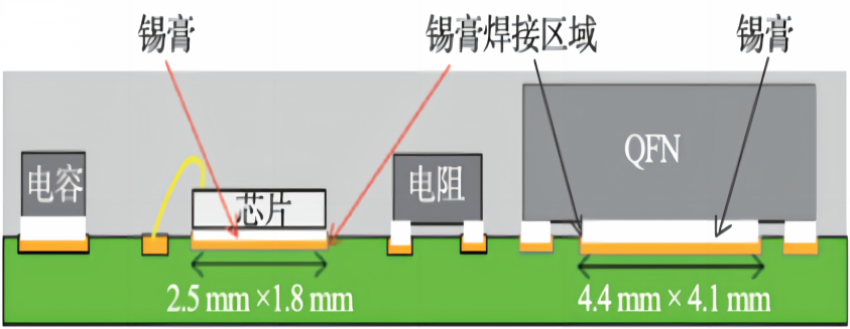
Dibuixos de soldadura QFN i de xapa nua
Per facilitar la comparació dels resultats de les proves, la soldadura per refusió es va realitzar en les condicions de la Taula 2.
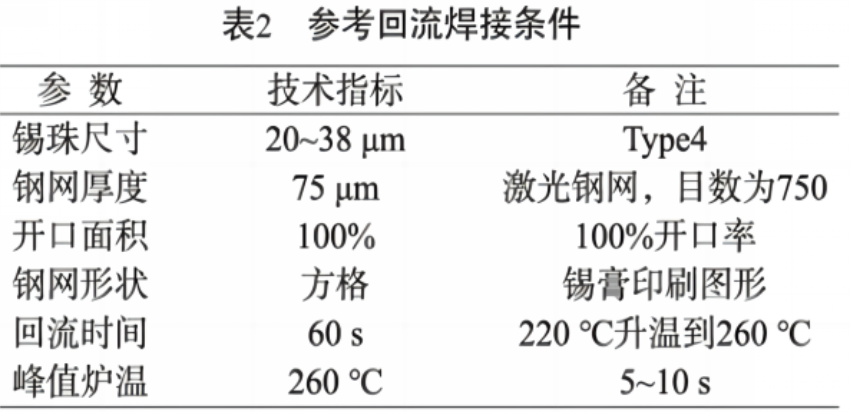
Taula de condicions de soldadura per refusió
Després de completar el muntatge superficial i la soldadura per refusió, la capa de soldadura es va detectar mitjançant raigs X i es va trobar que hi havia grans forats a la capa de soldadura a la part inferior del QFN i a la xip nua, tal com es mostra a la Figura 5.
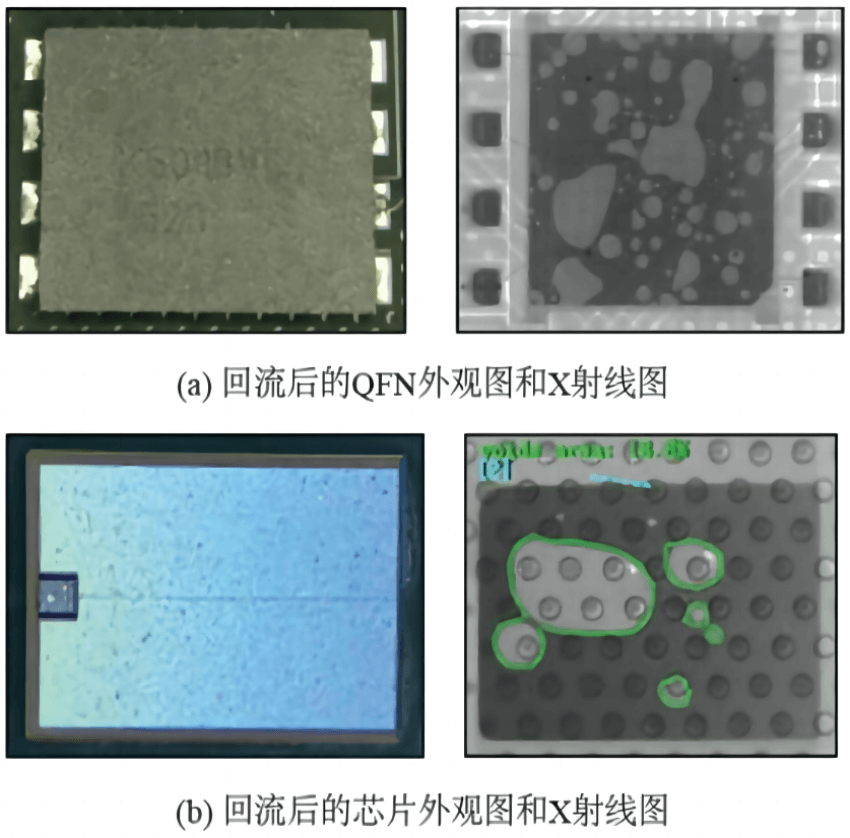
QFN i holograma de xip (raigs X)
Com que la mida del cordó d'estany, el gruix de la malla d'acer, la velocitat de l'àrea d'obertura, la forma de la malla d'acer, el temps de reflux i la temperatura màxima del forn afectaran els buits de soldadura per reflux, hi ha molts factors d'influència, que es verificaran directament mitjançant la prova DOE, i el nombre de grups experimentals serà massa gran. Cal cribrar i determinar ràpidament els principals factors d'influència mitjançant la prova de comparació de correlació i, a continuació, optimitzar encara més els principals factors d'influència mitjançant DOE.
3.1 Dimensions dels forats de soldadura i de les perles d'estany de pasta de soldadura
Amb la prova de pasta de soldadura SAC305 de tipus 3 (mida de cordó 25-45 μm), la resta de condicions romanen sense canvis. Després de la refusió, es mesuren els forats de la capa de soldadura i es comparen amb la pasta de soldadura de tipus 4. Es constata que els forats de la capa de soldadura no són significativament diferents entre els dos tipus de pasta de soldadura, cosa que indica que la pasta de soldadura amb diferents mides de cordó no té cap influència òbvia en els forats de la capa de soldadura, cosa que no és un factor influent, com es mostra a la FIG. 6.
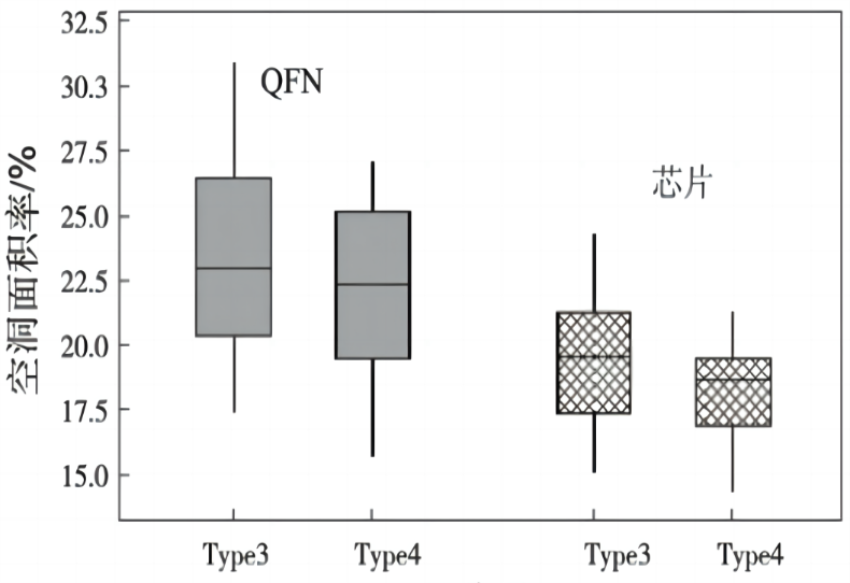
Comparació de forats de pols d'estany metàl·lic amb diferents mides de partícula
3.2 Gruix de la cavitat de soldadura i de la malla d'acer impresa
Després de la refusió, es va mesurar l'àrea de la cavitat de la capa soldada amb la malla d'acer impresa amb un gruix de 50 μm, 100 μm i 125 μm, i la resta de condicions es van mantenir sense canvis. Es va trobar que l'efecte dels diferents gruixos de la malla d'acer (pasta de soldadura) sobre la QFN es va comparar amb el de la malla d'acer impresa amb un gruix de 75 μm. A mesura que augmenta el gruix de la malla d'acer, l'àrea de la cavitat disminueix gradualment. Després d'assolir un cert gruix (100 μm), l'àrea de la cavitat s'invertirà i començarà a augmentar amb l'augment del gruix de la malla d'acer, tal com es mostra a la Figura 7.
Això demostra que quan augmenta la quantitat de pasta de soldadura, l'estany líquid amb reflux queda cobert pel xip, i la sortida de l'aire residual només és estreta en quatre costats. Quan canvia la quantitat de pasta de soldadura, la sortida de l'aire residual també augmenta, i l'explosió instantània d'aire embolicat en estany líquid o gas volàtil que s'escapa de l'estany líquid farà que l'estany líquid esquitxi al voltant del QFN i del xip.
La prova va trobar que amb l'augment del gruix de la malla d'acer, també augmentarà l'esclat de bombolles causat per l'escapament d'aire o gas volàtil, i la probabilitat que esquitxi estany al voltant del QFN i l'encenall també augmentarà en conseqüència.
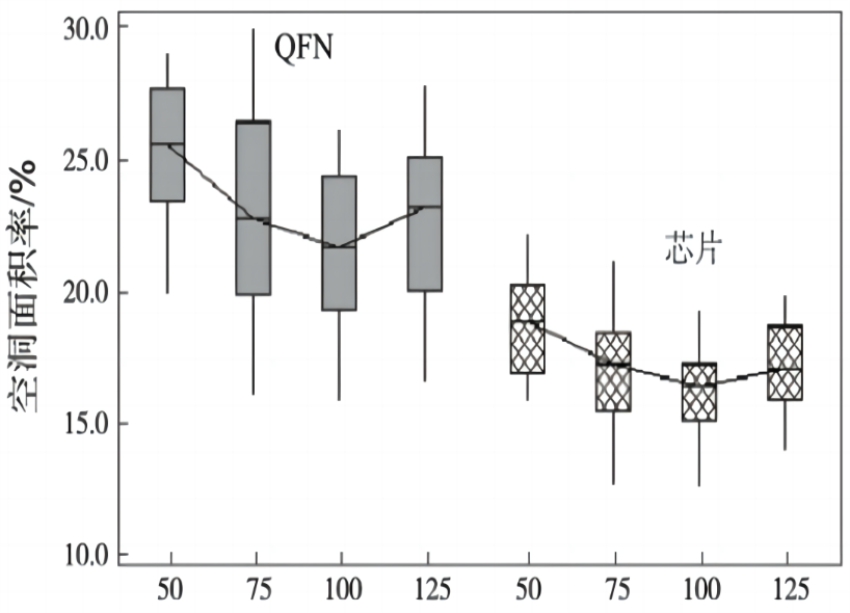
Comparació de forats en malla d'acer de diferents gruixos
3.3 Relació d'àrea de la cavitat de soldadura i l'obertura de la malla d'acer
Es va provar la malla d'acer impresa amb una taxa d'obertura del 100%, 90% i 80%, i la resta de condicions es van mantenir sense canvis. Després de la refusió, es va mesurar l'àrea de la cavitat de la capa soldada i es va comparar amb la malla d'acer impresa amb una taxa d'obertura del 100%. Es va trobar que no hi havia cap diferència significativa en la cavitat de la capa soldada en les condicions de taxa d'obertura del 100% i del 90%-80%, tal com es mostra a la Figura 8.
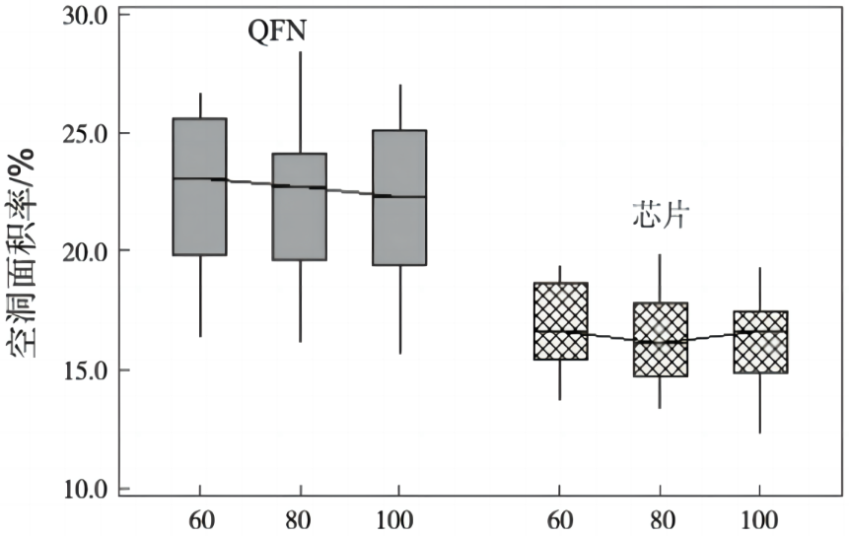
Comparació de cavitats de diferents àrees d'obertura de diferents malles d'acer
3.4 Cavitat soldada i forma de malla d'acer impresa
Amb la prova de forma d'impressió de la pasta de soldadura de la tira b i la malla inclinada c, la resta de condicions romanen sense canvis. Després de la refusió, es mesura l'àrea de la cavitat de la capa de soldadura i es compara amb la forma d'impressió de la malla a. Es constata que no hi ha cap diferència significativa a la cavitat de la capa de soldadura en les condicions de la malla, la tira i la malla inclinada, tal com es mostra a la Figura 9.
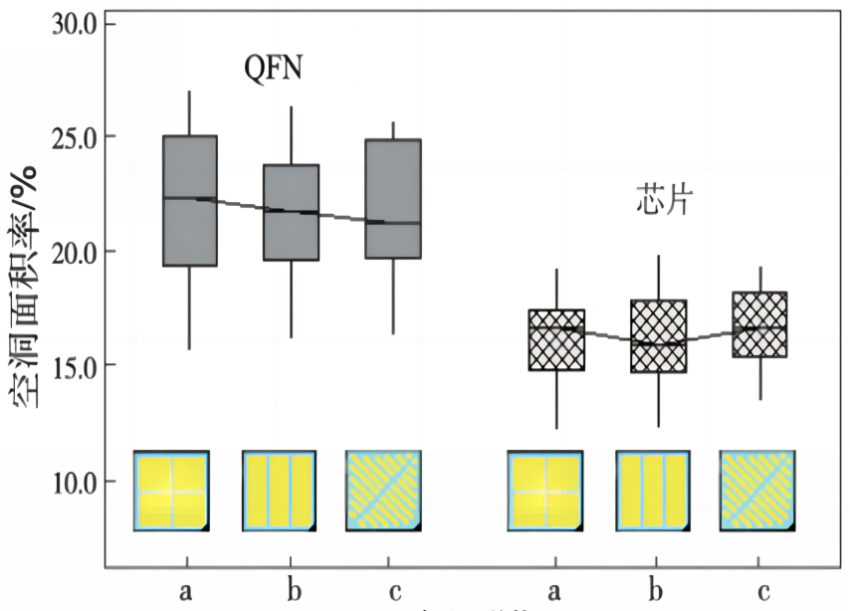
Comparació de forats en diferents modes d'obertura de malla d'acer
3.5 Cavitat de soldadura i temps de reflux
Després d'una prova de temps de reflux prolongat (70 s, 80 s, 90 s), la resta de condicions romanen sense canvis. Es va mesurar el forat a la capa de soldadura després del reflux i, en comparació amb el temps de reflux de 60 s, es va trobar que amb l'augment del temps de reflux, l'àrea del forat de soldadura disminuïa, però l'amplitud de reducció disminuïa gradualment amb l'augment del temps, com es mostra a la Figura 10. Això demostra que en el cas d'un temps de reflux insuficient, augmentar el temps de reflux afavoreix el desbordament complet de l'aire embolicat en l'estany líquid fos, però després que el temps de reflux augmenti fins a un cert temps, l'aire embolicat en l'estany líquid és difícil que es torni a desbordar. El temps de reflux és un dels factors que afecten la cavitat de soldadura.
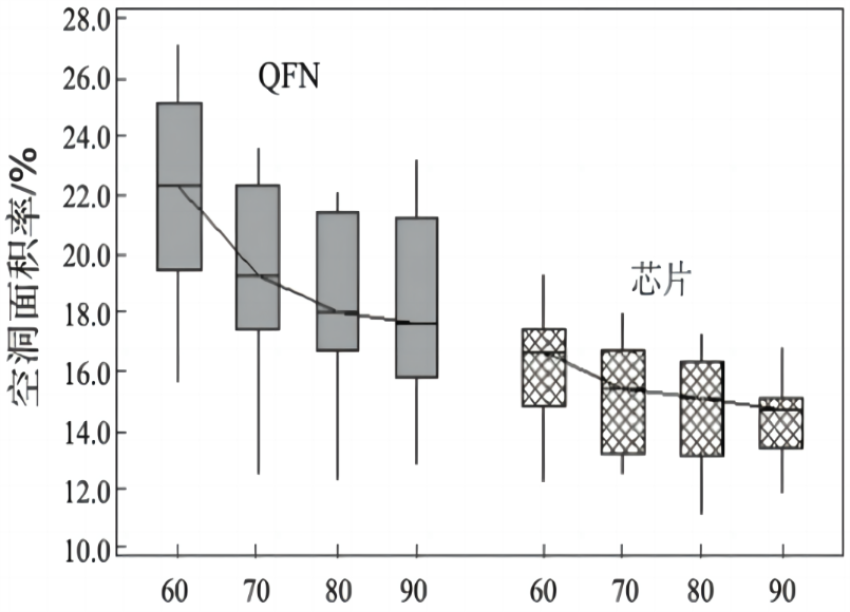
Comparació de buits de diferents durades de temps de reflux
3.6 Cavitat de soldadura i temperatura màxima del forn
Amb proves de temperatura màxima del forn de 240 ℃ i 250 ℃ i altres condicions sense canvis, es va mesurar l'àrea de la cavitat de la capa soldada després de la refusió i, en comparació amb la temperatura màxima del forn de 260 ℃, es va trobar que, en diferents condicions de temperatura màxima del forn, la cavitat de la capa soldada de QFN i el xip no va canviar significativament, com es mostra a la Figura 11. Mostra que les diferents temperatures màximes del forn no tenen cap efecte evident sobre QFN i el forat a la capa de soldadura del xip, cosa que no és un factor influent.
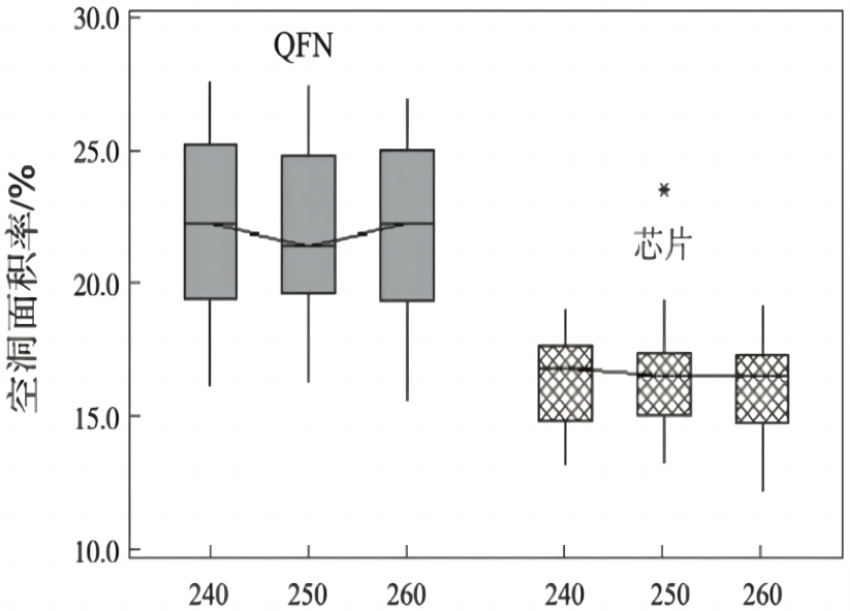
Comparació buida de diferents temperatures màximes
Les proves anteriors indiquen que els factors significatius que afecten la cavitat de la capa de soldadura de QFN i l'encenall són el temps de reflux i el gruix de la malla d'acer.
4 Millora de la cavitat de soldadura per refusió amb pasta de soldadura per impressió
Prova 4.1DOE per millorar la cavitat de soldadura
El forat a la capa de soldadura de QFN i xip es va millorar trobant el valor òptim dels principals factors d'influència (temps de reflux i gruix de la malla d'acer). La pasta de soldadura era SAC305 tipus 4, la forma de la malla d'acer era de tipus quadrícula (grau d'obertura del 100%), la temperatura màxima del forn era de 260 ℃ i les altres condicions de prova van ser les mateixes que les de l'equip de prova. La prova DOE i els resultats es mostren a la Taula 3. Les influències del gruix de la malla d'acer i el temps de reflux en els forats de soldadura de QFN i xip es mostren a la Figura 12. Mitjançant l'anàlisi d'interacció dels principals factors d'influència, es va trobar que l'ús d'un gruix de malla d'acer de 100 μm i un temps de reflux de 80 s pot reduir significativament la cavitat de soldadura de QFN i xip. La taxa de cavitat de soldadura de QFN es redueix del màxim del 27,8% al 16,1%, i la taxa de cavitat de soldadura de xip es redueix del màxim del 20,5% al 14,5%.
A la prova, es van produir 1000 productes en condicions òptimes (gruix de malla d'acer de 100 μm, temps de reflux de 80 s), i la taxa de cavitat de soldadura de 100 QFN i xip es va mesurar aleatòriament. La taxa mitjana de cavitat de soldadura de QFN va ser del 16,4% i la taxa mitjana de cavitat de soldadura de xip va ser del 14,7%. La taxa de cavitat de soldadura de l'xip i l'xip es redueix evidentment.
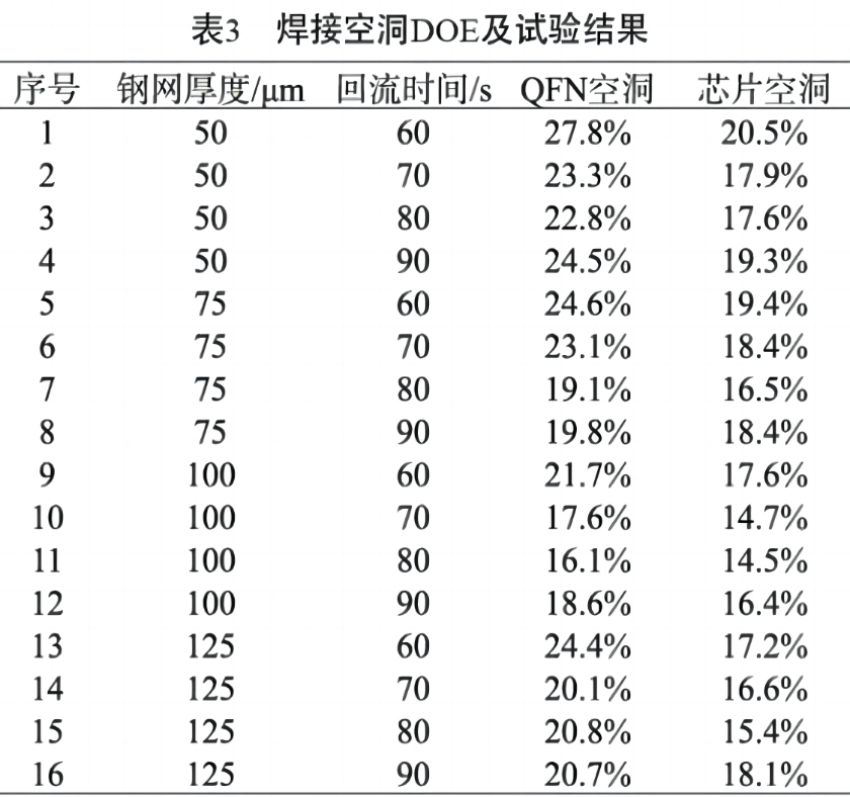
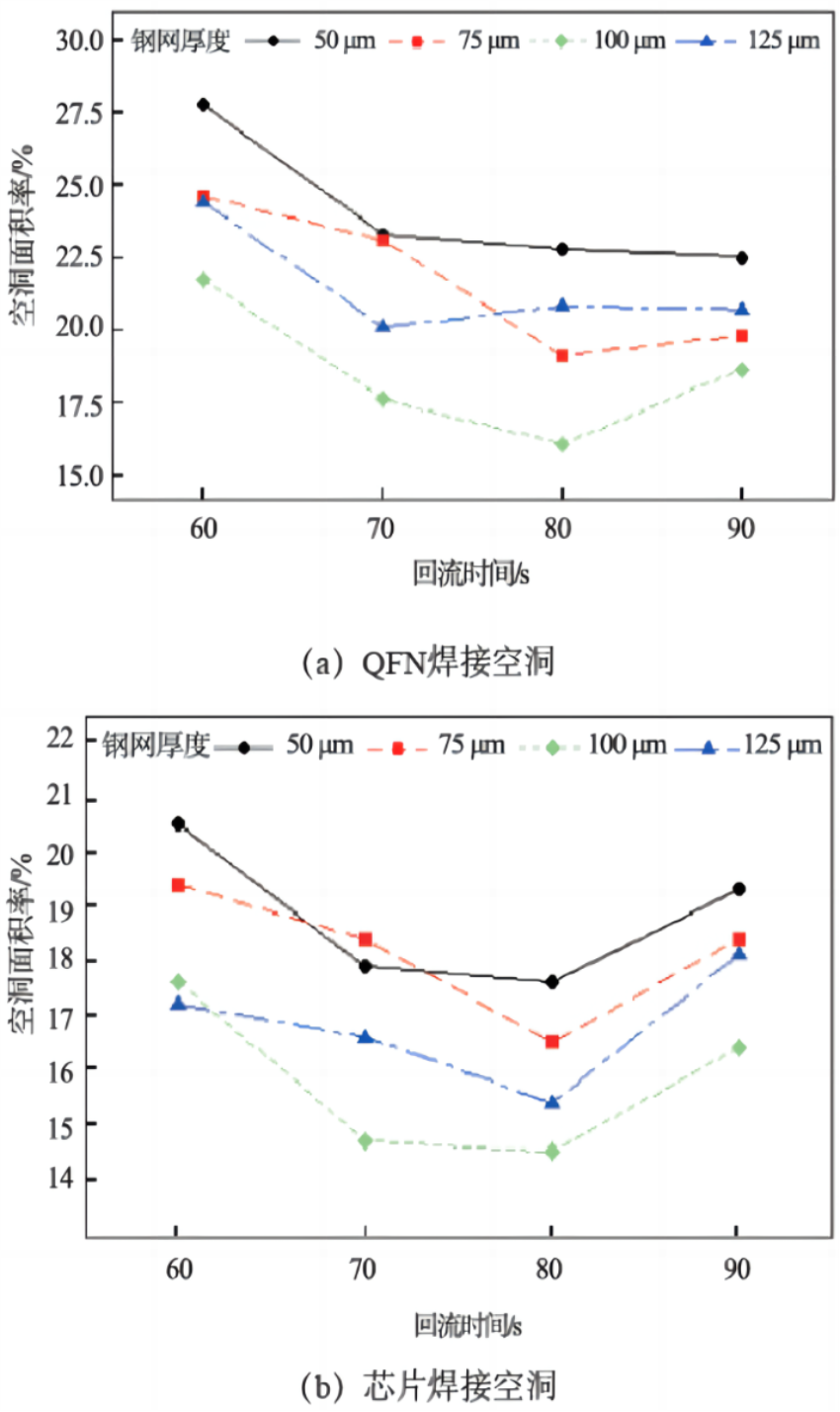
4.2 El nou procés millora la cavitat de soldadura
La situació de producció real i les proves mostren que quan l'àrea de la cavitat de soldadura a la part inferior del xip és inferior al 10%, el problema de la fissura de la posició de la cavitat del xip no es produirà durant la unió i el modelat del plom. Els paràmetres del procés optimitzats per DOE no poden complir els requisits d'anàlisi i resolució dels forats en la soldadura per refusió de pasta de soldadura convencional, i cal reduir encara més la taxa d'àrea de la cavitat de soldadura del xip.
Com que el xip cobert a la soldadura impedeix que el gas de la soldadura s'escapi, la taxa de forats a la part inferior del xip es redueix encara més eliminant o reduint el gas recobert de soldadura. S'adopta un nou procés de soldadura per reflux amb dues impressions de pasta de soldadura: una impressió de pasta de soldadura, una reflux que no cobreix QFN i xip nu que descarrega el gas a la soldadura; El procés específic d'impressió secundària de pasta de soldadura, pegat i reflux secundari es mostra a la Figura 13.
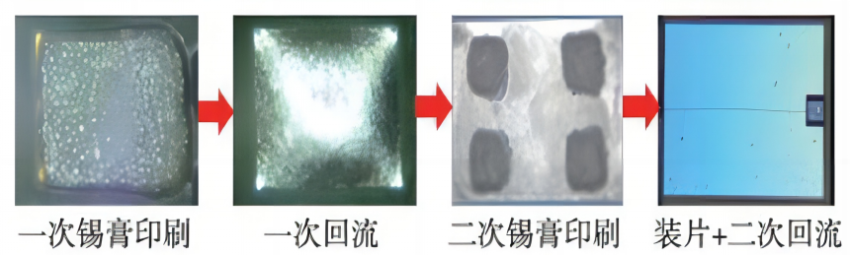
Quan s'imprimeix per primera vegada pasta de soldadura de 75 μm de gruix, la major part del gas de la soldadura sense cobertura de xip s'escapa de la superfície, i el gruix després del reflux és d'uns 50 μm. Després de completar el reflux primari, s'imprimeixen petits quadrats a la superfície de la soldadura solidificada refredada (per tal de reduir la quantitat de pasta de soldadura, reduir la quantitat de vessament de gas, reduir o eliminar les esquitxades de soldadura), i la pasta de soldadura amb un gruix de 50 μm (els resultats de la prova anterior mostren que 100 μm és el millor, de manera que el gruix de la impressió secundària és de 100 μm. 50 μm = 50 μm), després instal·leu el xip i torneu a passar 80 s. Gairebé no hi ha forats a la soldadura després de la primera impressió i reflux, i la pasta de soldadura a la segona impressió és petita i el forat de soldadura és petit, com es mostra a la Figura 14.
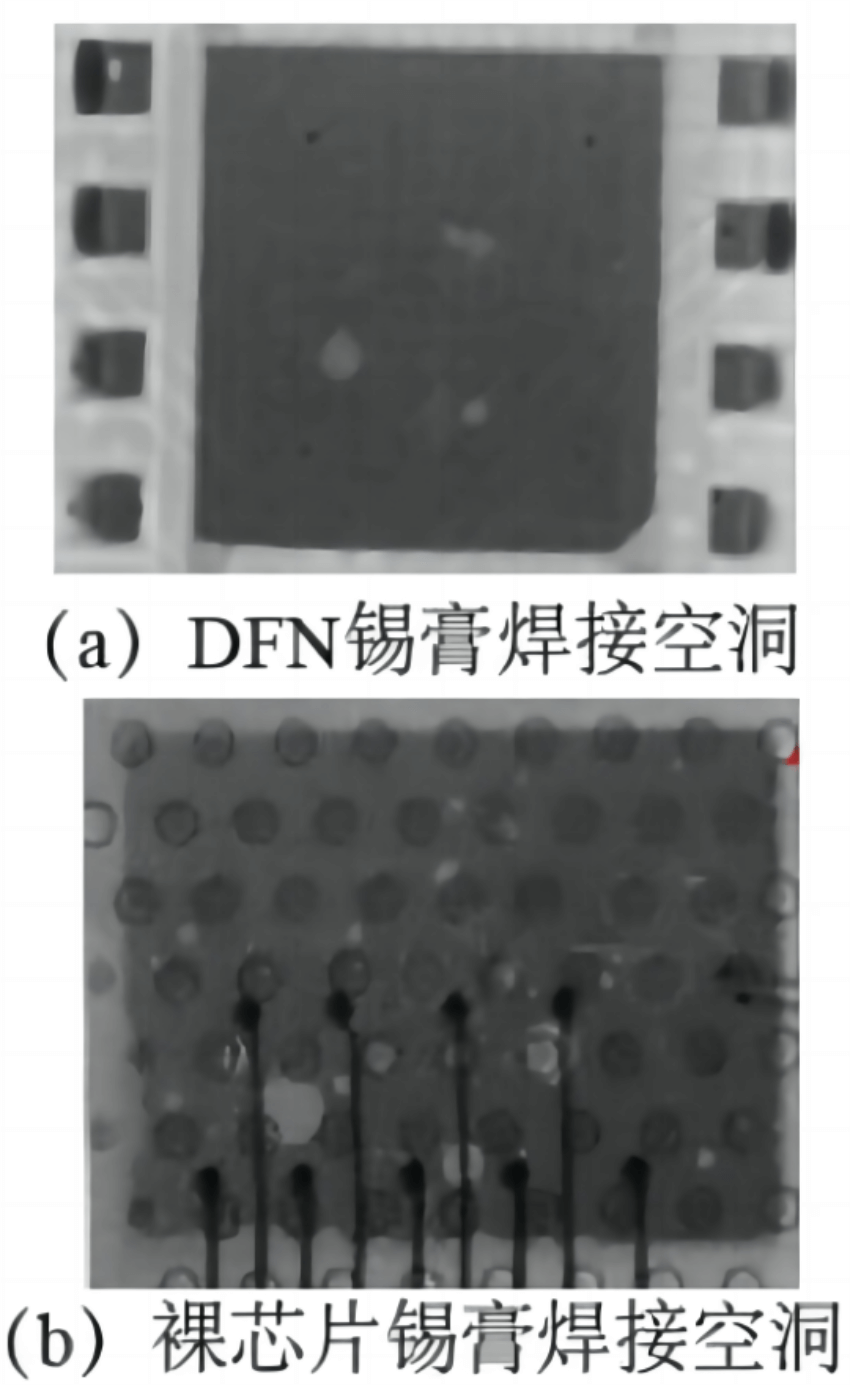
Després de dues impressions de pasta de soldadura, dibuix buit
4.3 Verificació de l'efecte de la cavitat de soldadura
Producció de 2000 productes (el gruix de la primera malla d'acer d'impressió és de 75 μm, el gruix de la segona malla d'acer d'impressió és de 50 μm), altres condicions sense canvis, mesurament aleatori de 500 QFN i taxa de cavitat de soldadura de xip, es va trobar que el nou procés després del primer reflux no hi havia cavitat, després del segon QFN de reflux la taxa màxima de cavitat de soldadura és del 4,8% i la taxa màxima de cavitat de soldadura del xip és del 4,1%. En comparació amb el procés de soldadura d'impressió de pasta única original i el procés optimitzat DOE, la cavitat de soldadura es redueix significativament, com es mostra a la Figura 15. No es van trobar esquerdes de xip després de les proves funcionals de tots els productes.
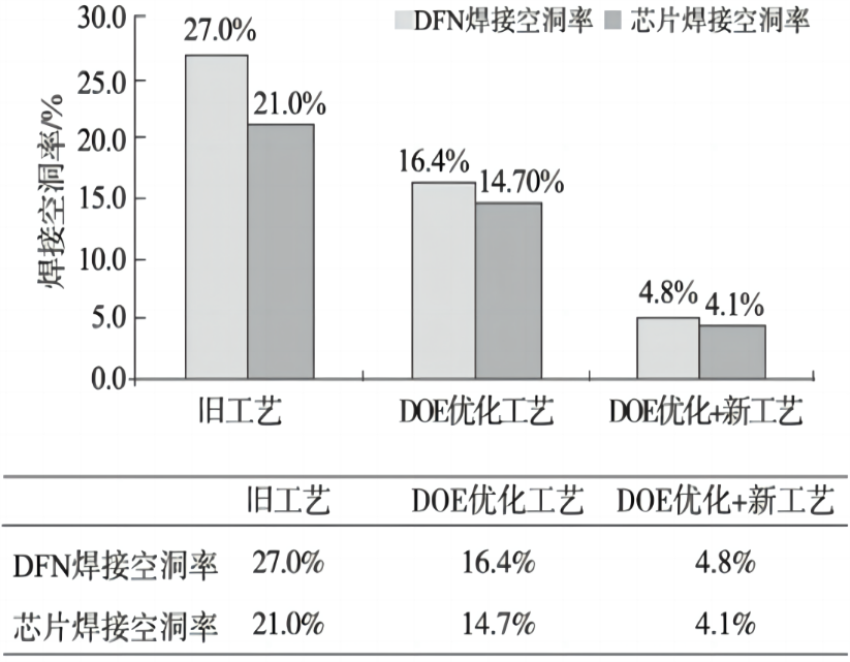
5 Resum
L'optimització de la quantitat d'impressió de pasta de soldadura i el temps de reflux pot reduir l'àrea de la cavitat de soldadura, però la velocitat de la cavitat de soldadura continua sent gran. L'ús de dues tècniques de soldadura per reflux amb impressió de pasta de soldadura pot maximitzar de manera efectiva la velocitat de la cavitat de soldadura. L'àrea de soldadura del xip nu del circuit QFN pot ser de 4,4 mm x 4,1 mm i 3,0 mm x 2,3 mm respectivament en la producció en massa. La velocitat de la cavitat de la soldadura per reflux es controla per sota del 5%, cosa que millora la qualitat i la fiabilitat de la soldadura per reflux. La investigació d'aquest article proporciona una referència important per millorar el problema de la cavitat de soldadura en superfícies de soldadura de grans dimensions.